Performance monitoring for efficiency of drilling operations
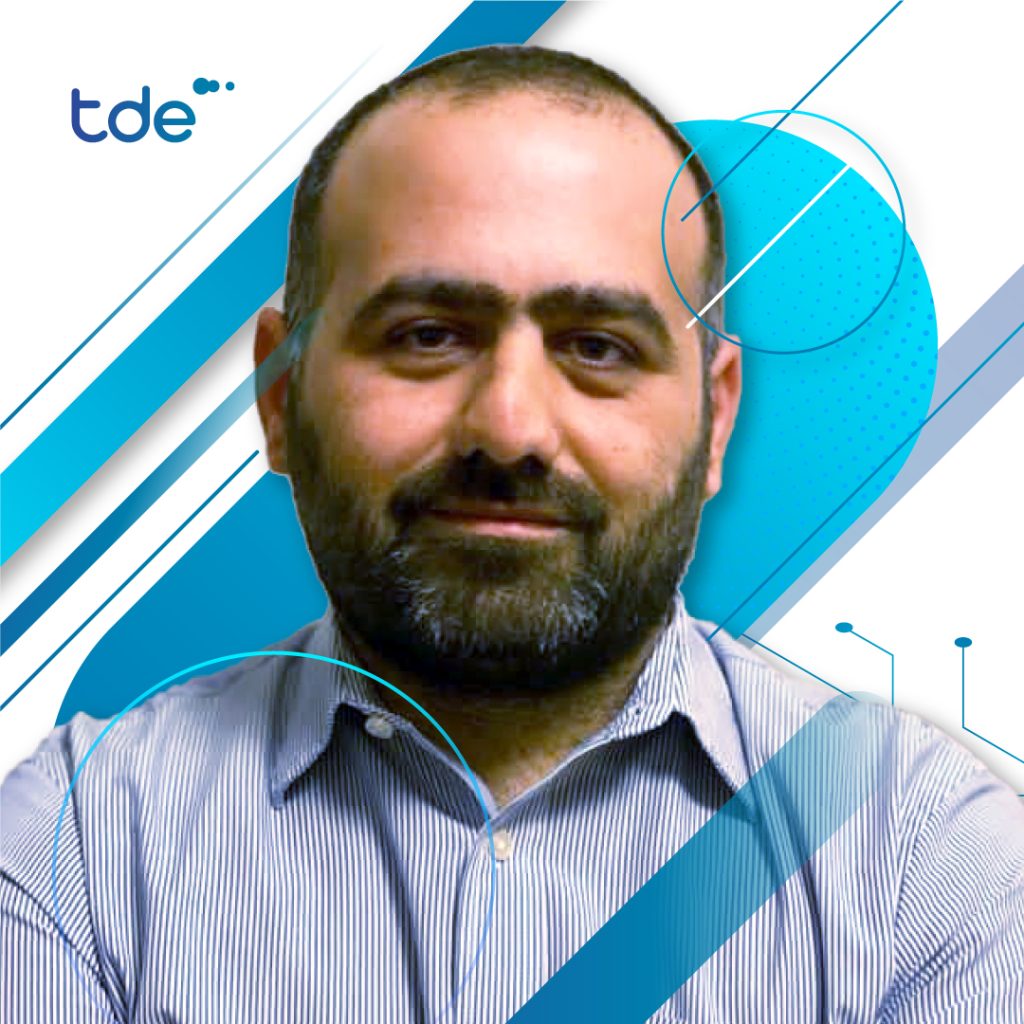
Tural Garibov
Regional Sales Manager @ tde driving digital transformation in energy
Share on:
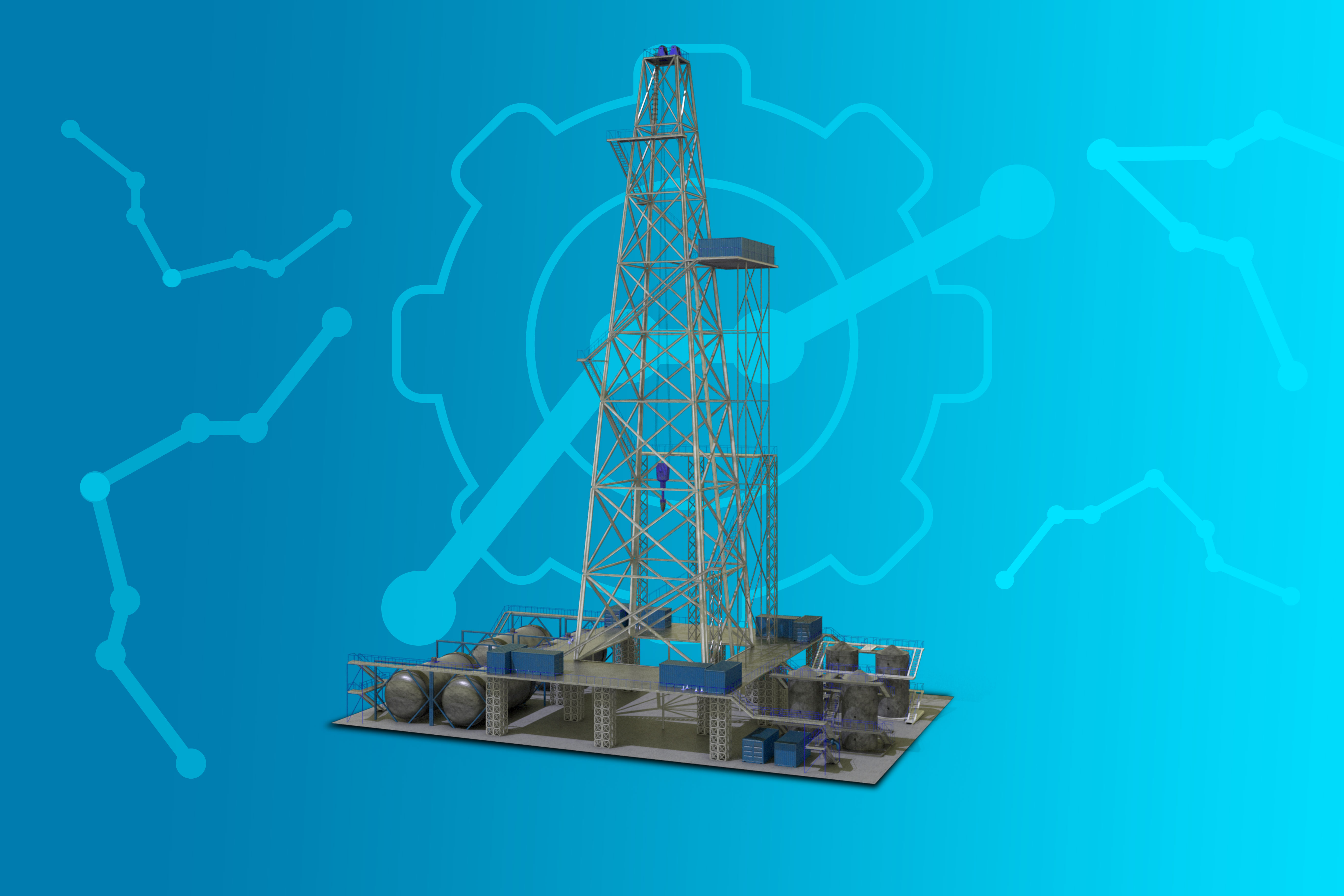
Introduction
In the dynamic world of oil and gas extraction, everyone faces the challenge of optimizing drilling operations to ensure both efficiency and cost-effectiveness. While established operators benefit from sophisticated drilling engineering solutions, emerging operators often find themselves navigating through the complexities without having the luxury of time, resources or dedicated tools like real-time operating centers (RTOCs). This gap frequently results in hindering productivity and profitability for the latter. I’ll try to summarize below how performance monitoring with tde pronova can bring significant change and advantage to such operators at a minimum cost.
The challenge
Emerging operators possess extensive knowledge of drilling engineering solutions, but often lack the capacity to establish an RTOC from scratch. Reasons for that can be same as mentioned above. But without data streaming and processing, they miss the benefits not because of the lack of an RTOC, but because the insights from data are left untouched. If no relevant industry solution is used to analyze the drilling data and it’s done manually, this task becomes cumbersome, time consuming and with open questions on data quality control and its integrity.
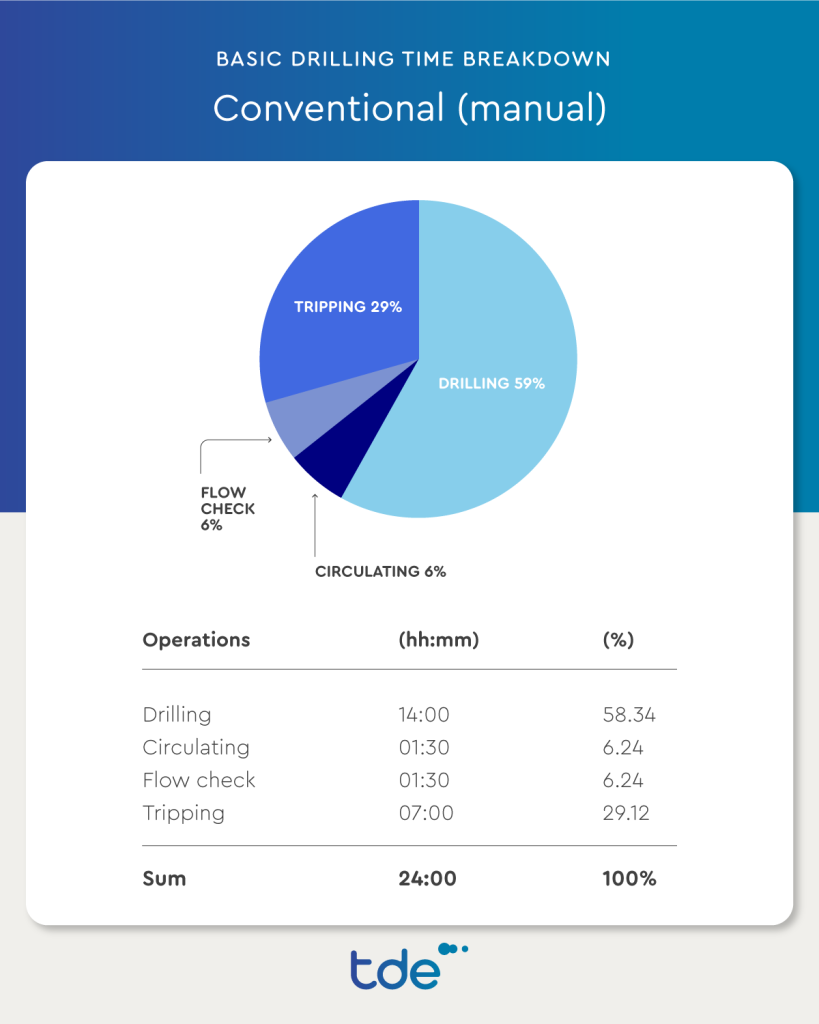
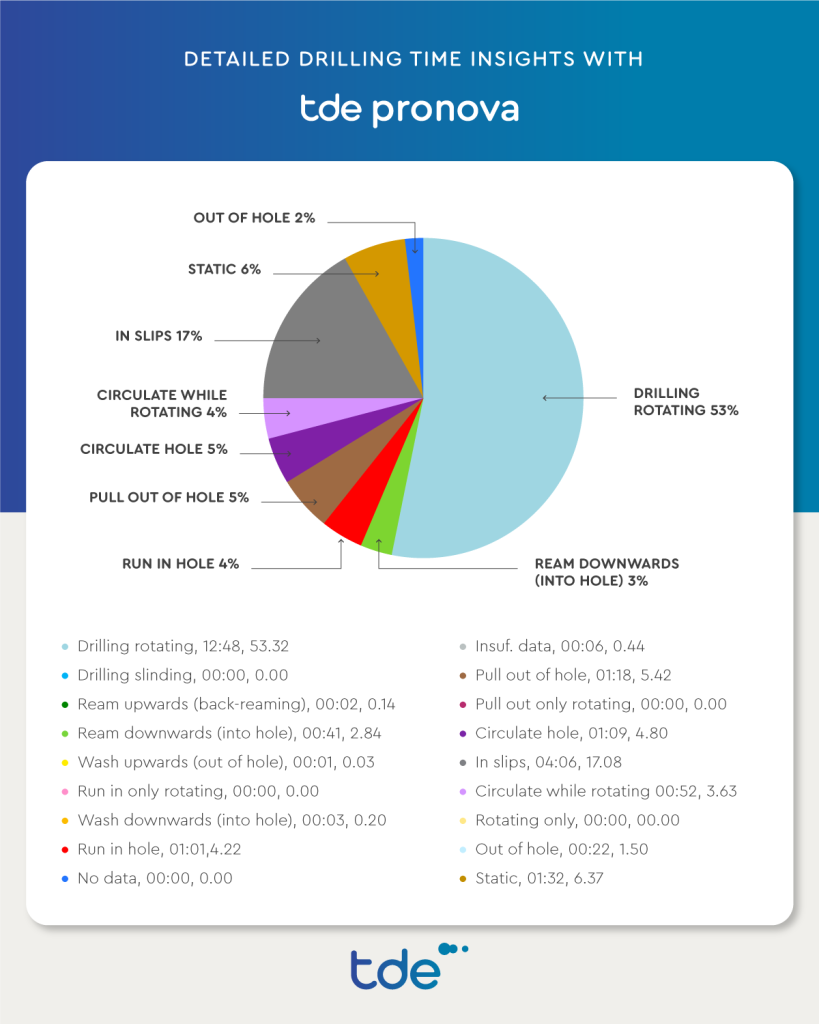
Performance monitoring benefits
Forward thinking
As technologies continue to advance, integration of performance monitoring solutions like tde pronova to drilling operations becomes essential. Looking ahead, embracing innovative technologies, exploring data-driven insights, and continuously optimizing drilling processes will be the key to staying competitive in the evolving landscape of E&P.
In conclusion, the benefits of performance monitoring are undeniable for those seeking to remove invisible loss time. Such technologies can help operators to embark on a journey towards enhanced efficiency, improved decision-making, and long-term sustainability, all while keeping their investment requirements to a minimum.