tde empower delivers data-driven insights for root-cause analysis of lost-in-hole event involving BHA components
Executive Summary
A drilling Bottom Hole Assembly (BHA) containing expensive components suffered severe damage, and parts of it were lost in the hole while drilling an onshore well. Drilling conditions and parameters appeared to be within normal ranges, and no red flags were observed during the drilling operations. Consequently, our customer requested tde’s team to perform a further analysis of the root cause.
Through tde empower data-driven well engineering, we were able to provide insights into the drilling environment and factors contributing to the failure. Additionally, we furnished necessary modifications in both well planning and drilling execution phases to prevent similar failures in the future.
Challenge
While using a 10 3⁄4-inch reamer to drill a tangent section in an onshore well, the Rotary Steerable System (RSS) was not actively steering; hence, it was not in used at this point. For this reason, it came as a surprise that the BHA had to be pulled out of the hole due to the loss of the RSS steering sleeves. Additionally, when pulled out of the hole, it was observed that the reamer’s arms were damaged, and one arm was lost in the hole. The damage to the reamer resulted in suboptimal wellbore quality and tight spots in the open hole.
As a consequence of this event, the rig lost 6.5 days of rig time. tde empower was engaged to conduct a further analysis of the root cause and find answers to the following questions:
1. How and why did the RSS sleeve get damaged and lost in the hole?
2. How and why did the reamer’s arms get damaged and lost in the hole?
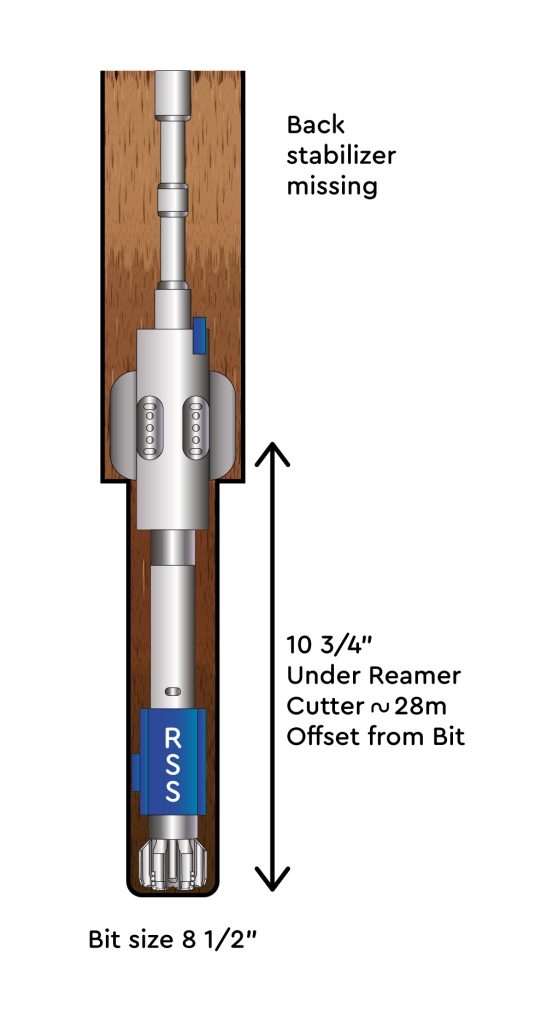
Solutions
Through a comprehensive post-run analysis, our data analysis and well engineering experts, tde empower team, identified areas for design and operational improvements in the existing BHA configuration which includes an 81⁄2” bit paired with a 103⁄4” reamer. In some cases, boreholes could be reamed at high RPMs during connections to move cuttings, but this practice should be avoided for a reamer BHA. The position and gauge of the RSS can sometimes be overlooked, particularly in the context of pilot and reamed sections. In this specific instance, during reaming back into the 81⁄2” pilot section, the three RSS sleeves acted as a full-gauged stabilizer, serving as the initial point of hard contact upon entering the pilot hole. After 45 drilling connections using this approach, the RSS ribs failed, likely due to repeated hard contacts against the ledge where the 81⁄2” pilot and the 103⁄4” reamed hole meets.
Results
Our tde empower team conducted a detailed contact force analysis for the reamer, revealing excessive side forces of 9 klbf on its cutting blades. This observation indicated that the BHA was not correctly stabilized. Further investigation led us to discover that the BHA lacked a top stabilizer. In other words, the reamer constituted the last hard contact point with the formation. Following well engineering best practices, we recommended placing an undergauged stabilizer above the reamer to prevent a fulcrum effect. Our experience has shown that such an effect could lead to twist-offs in deviated wells.
In summary, tde empower contributed to the following improvements:
1. Enhanced BHA design and stabilization of its components to reduce the risk of failure.
2. Optimized trajectory design to minimize high contact forces at the reamer.
3. Provided guidelines for using a reamer effectively, thereby avoiding premature failures.
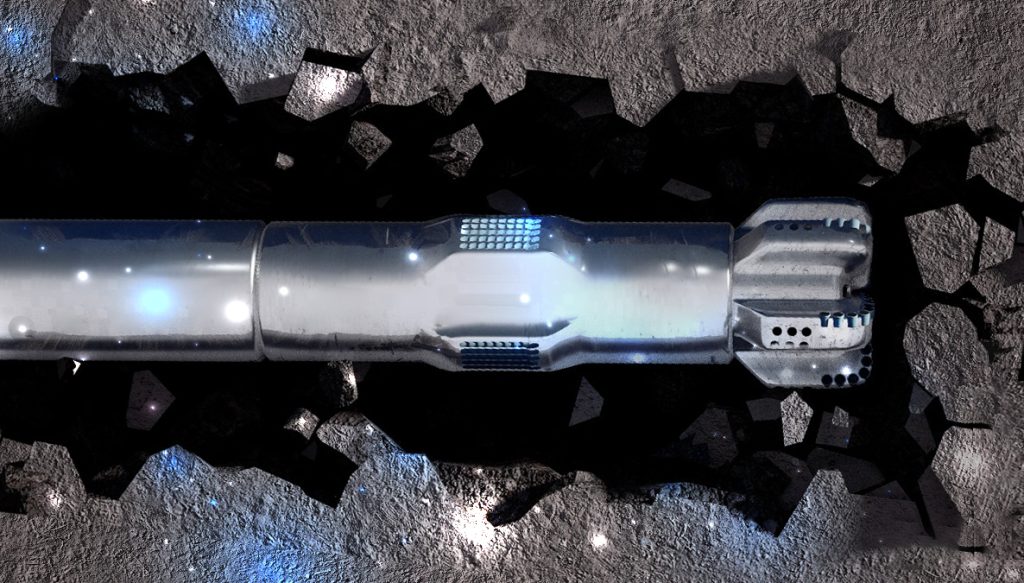