How a US-Land Operator used tde pronova solution to outperform KPI targets
How tde pronova helps
tde’s pronova brings together rigorous data QA/QC processes, comprehensive performance metrics and benchmarking methodologies, and enhanced reporting and analytics to increase operations’ visibility. Identifying and achieve best-safe-practices, to facilitate knowledge-sharing via the tde pronova real-time learning platform. By harboring an environment for excellence and “friendly competition”, tde pronova was able to assist across a two-year drilling campaign with five rigs for a US-Land Operator to improve operational efficiency that led to more than 130 days, or an estimated US$7.5 Million, in company savings.
Problems
Casing
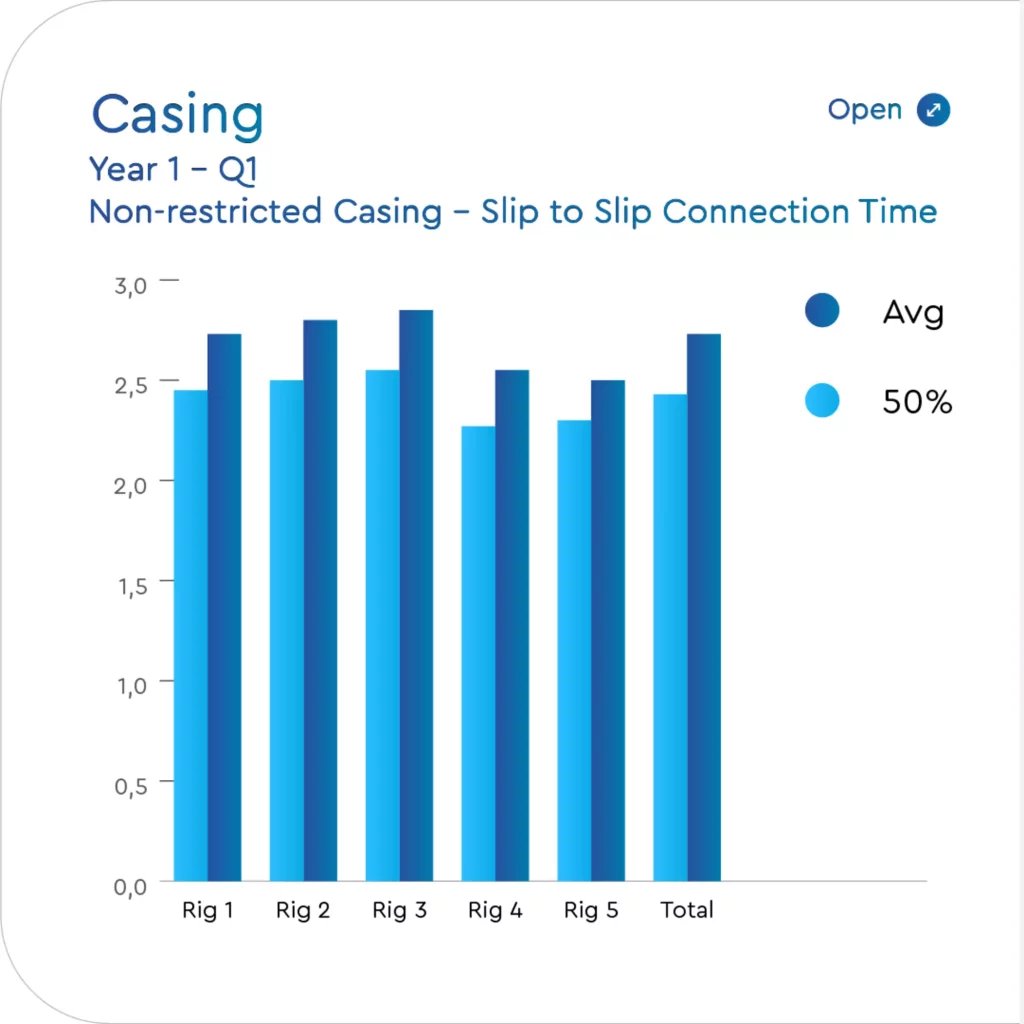
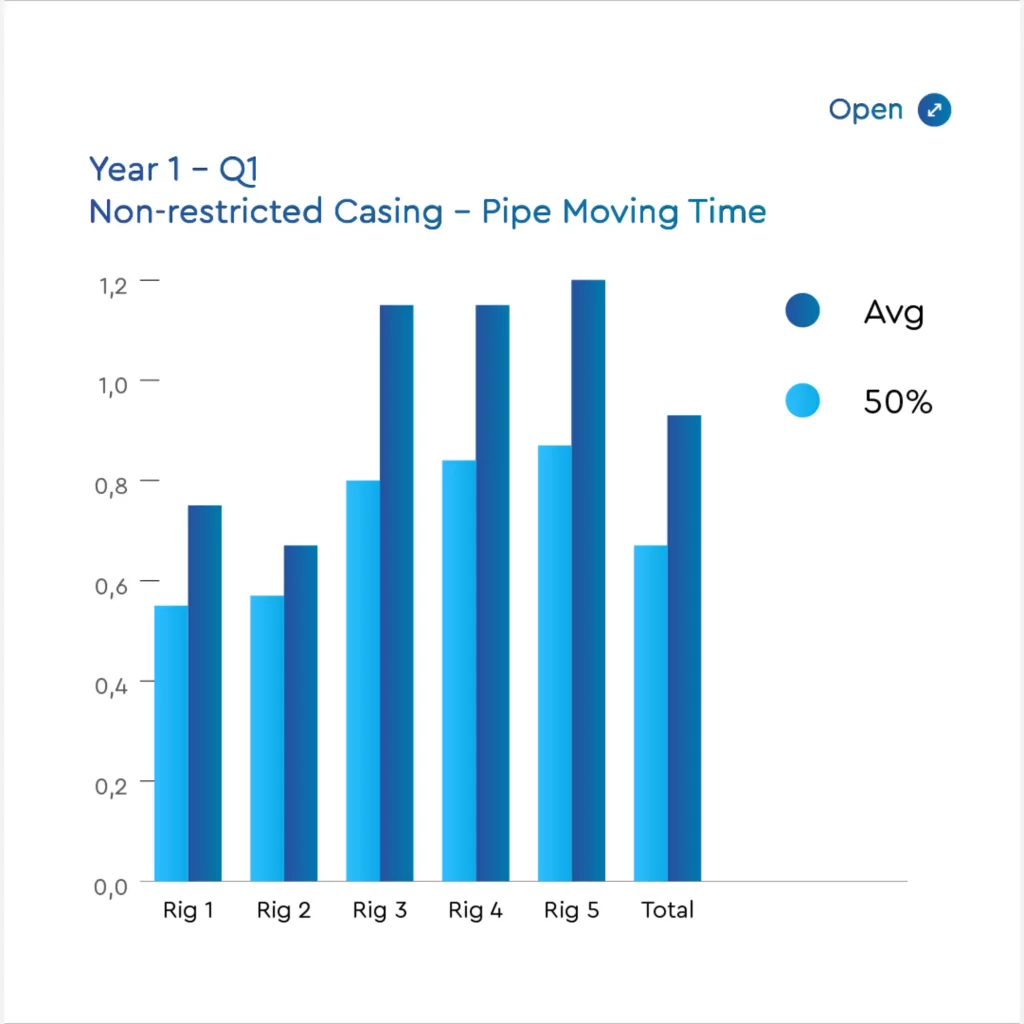
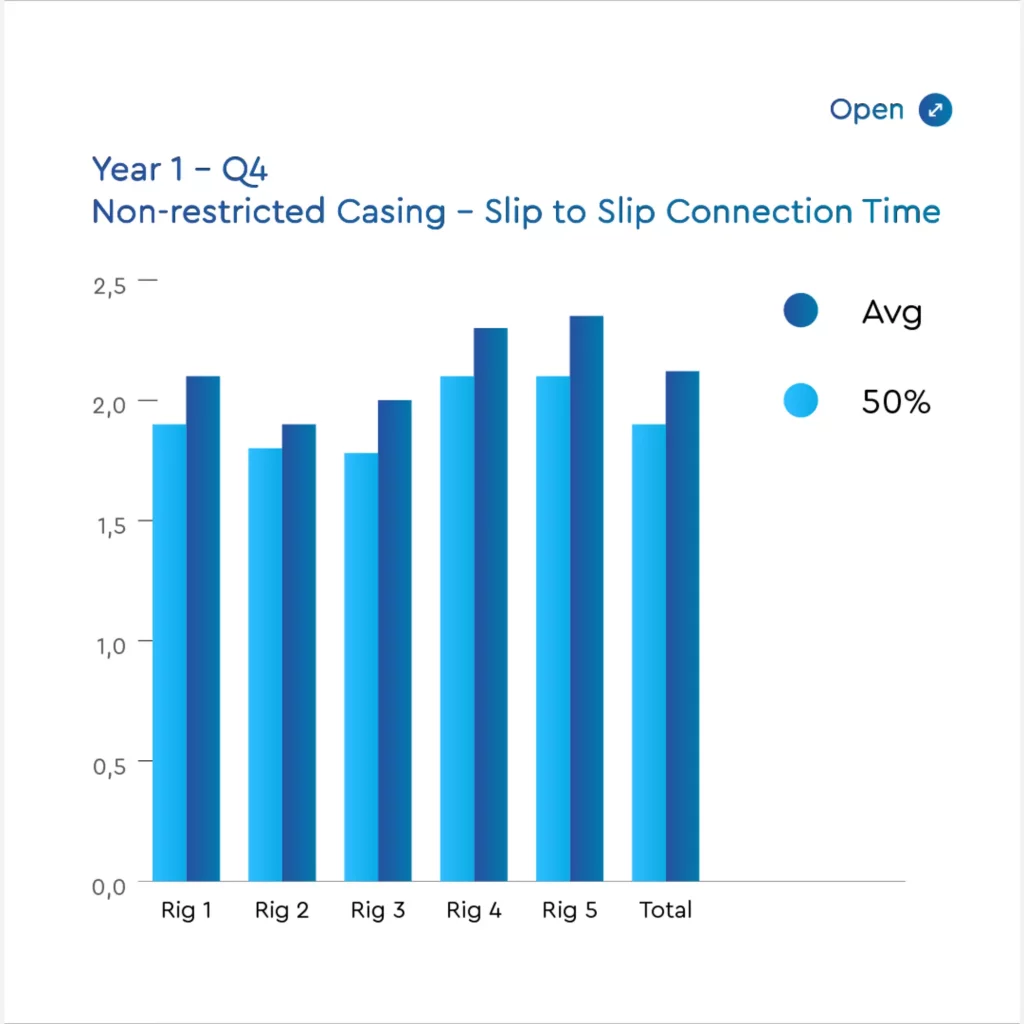
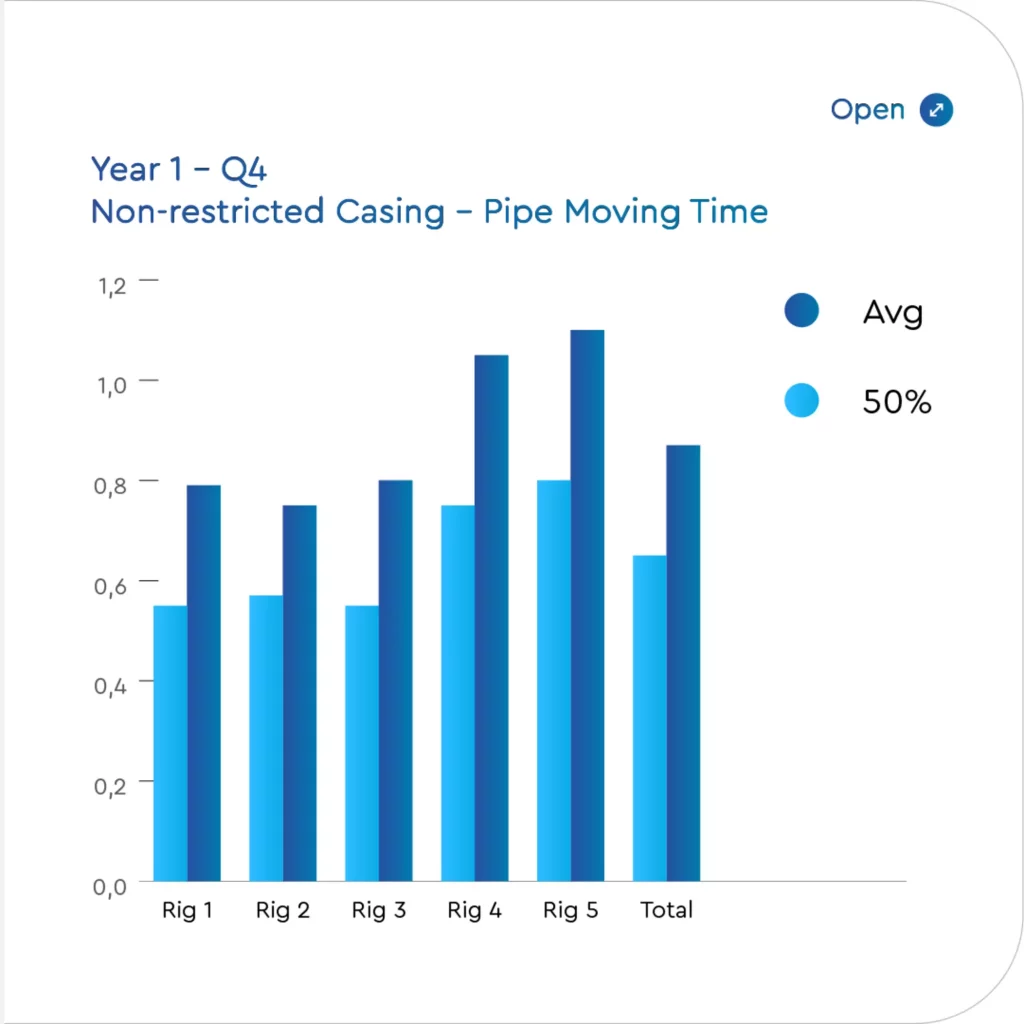
Tripping
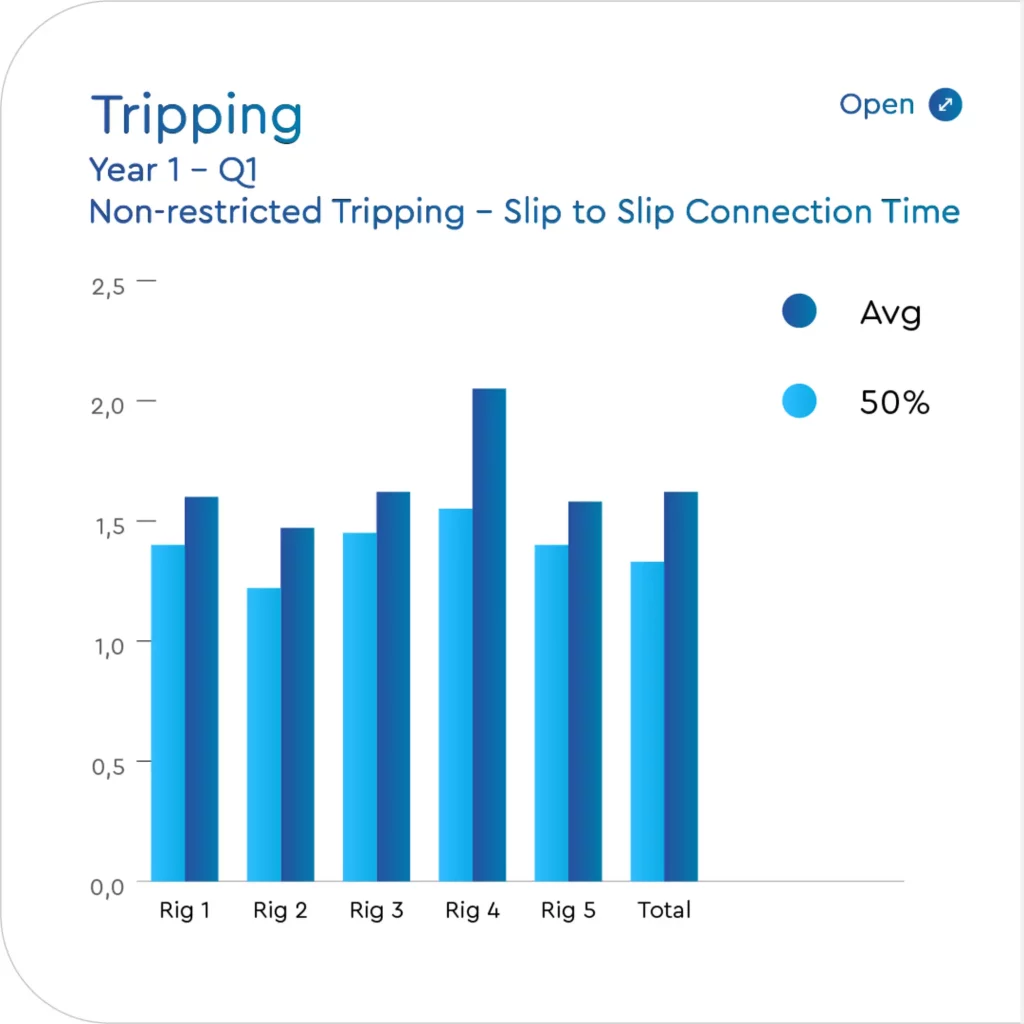
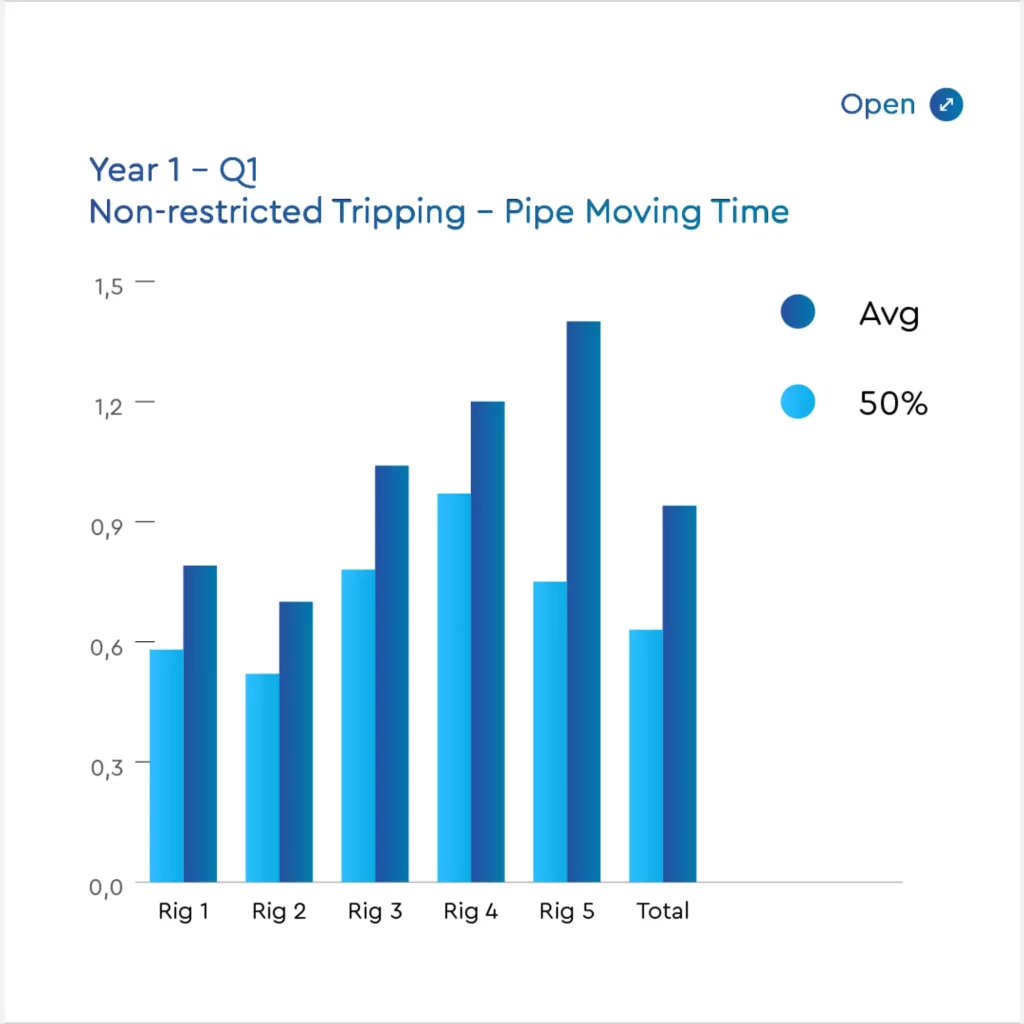
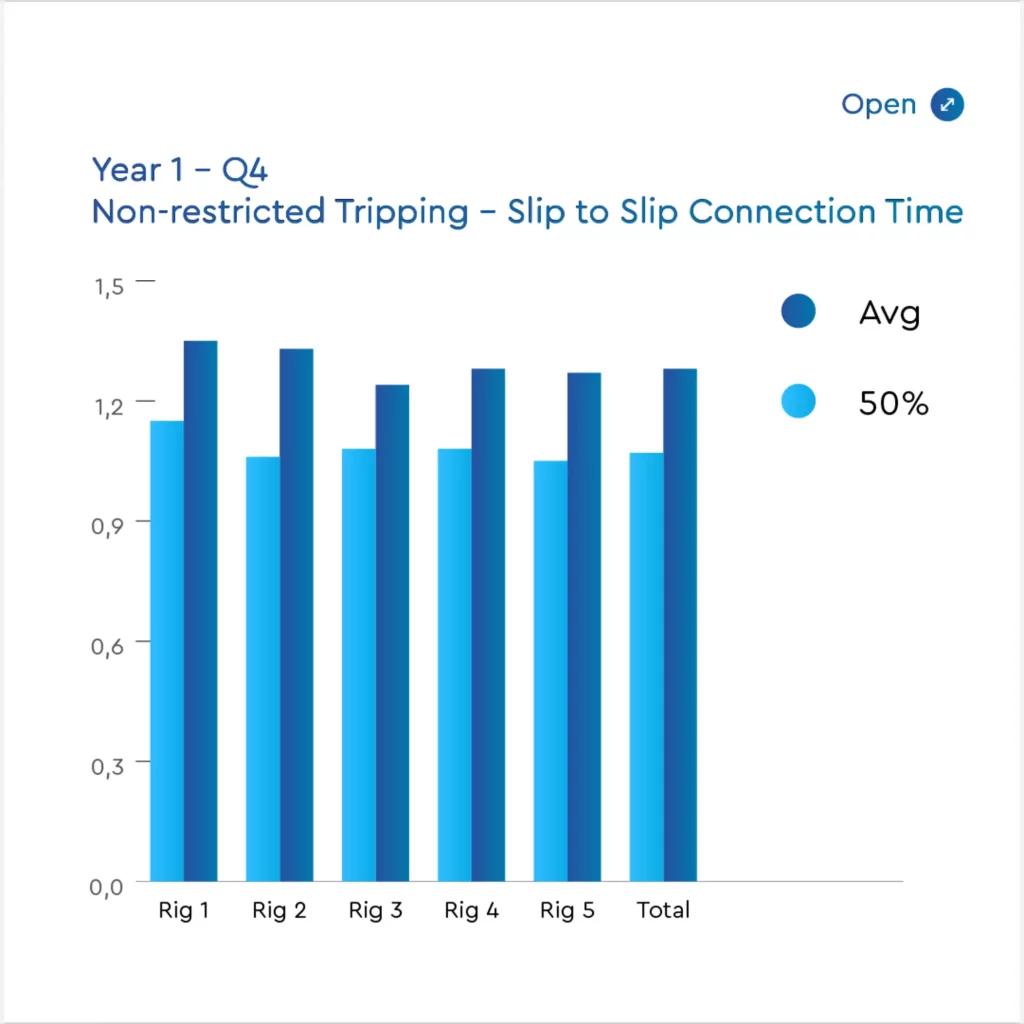
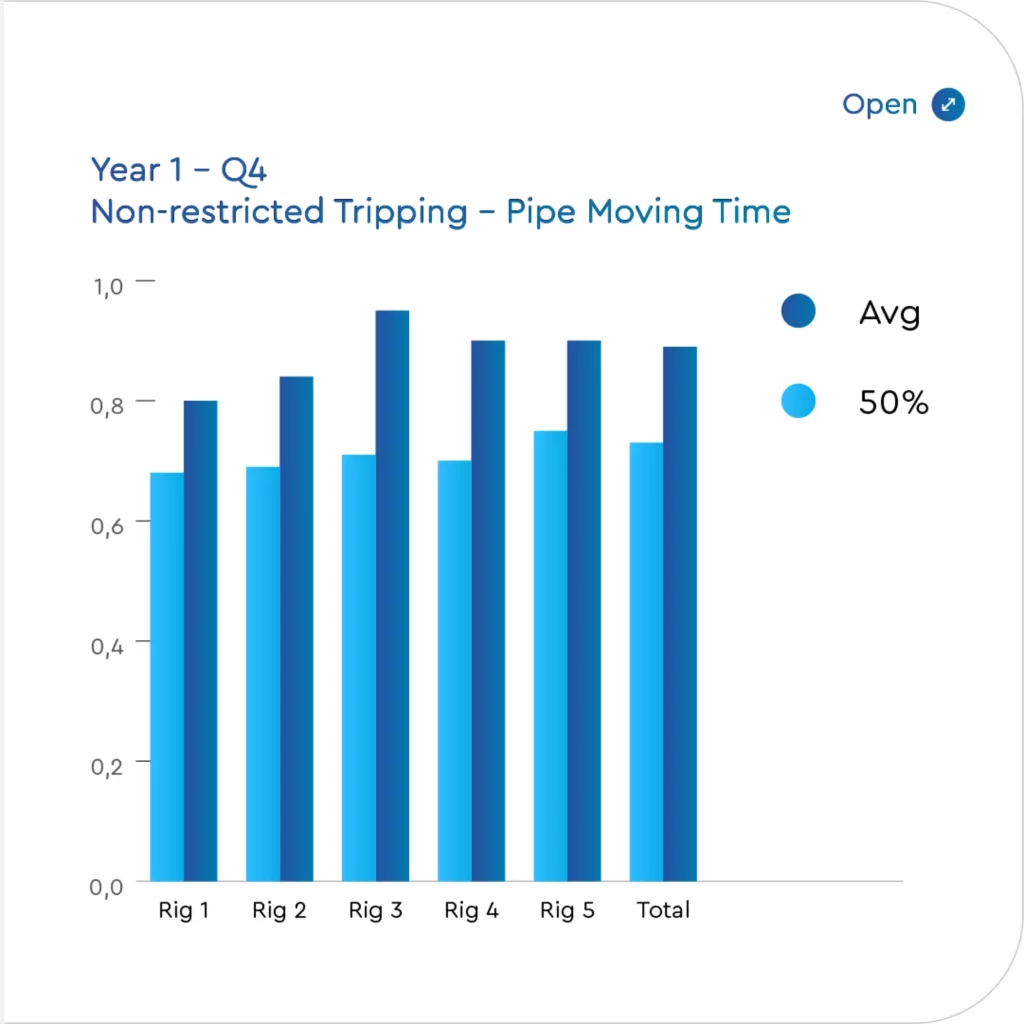
Drilling
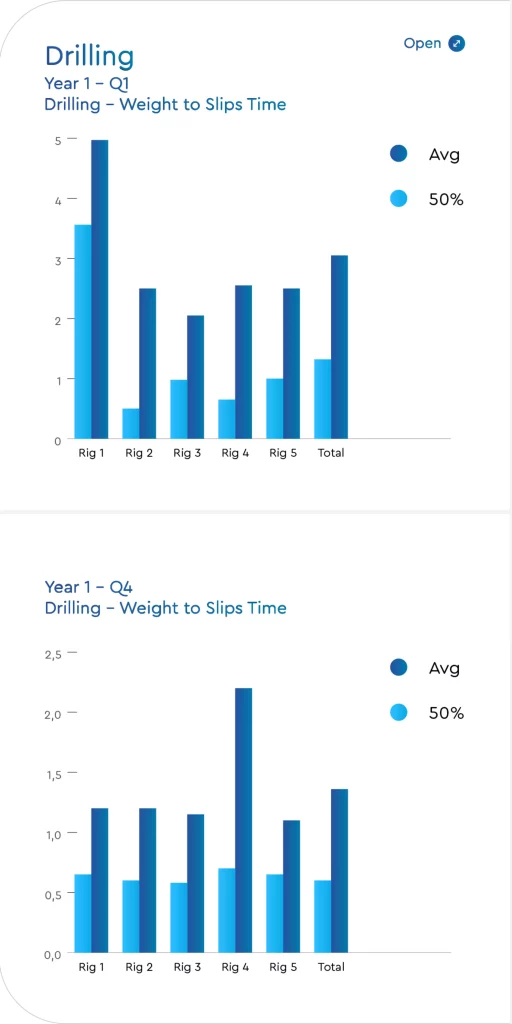


Approach
Managed roll-out: at the beginning of the campaign, the tde pronova solution captured data from each rig and established an objective baseline for a series of Key Performance Indicators using rig averages. This same dataset was used to identify best-safe-practice targets for each of the KPIs by reviewing each crew’s performance statistics. These baselines and targets were then communicated to all project stakeholders.
Daily Feedback: tde pronova client teams automated and sent a series of daily and weekly reports that guided stakeholders to highlight the highs and lows in performance to facilitate knowledge-sharing between crews and rigs during the morning safety briefings. In addition, tde pronova teams trained engineering and field personnel on the web-based application to help monitor activities in real-time and reference historical performance.
Field Involvement: specialized metrics centered around operational efficiency were generated based on KPI targets to ensure apples-to-apples comparisons between rigs. To further ensure equal comparisons between crews, tde pronova teams rigorously Quality Controlled (QC) drilling data and KPI results daily to ensure non-routine activities did not skew statistics.
Conclusion
To transform raw drilling data into actionable insights requires proven algorithms and robust quality-control. By combining proprietary rig-state detection and multi-tiered data QC, tde pronova added visibility and guidance that facilitated process maps and performance initiatives with the result of measurable efficiency improvements and significant savings to the operator.